Lynn_Pantic
Administrator
   
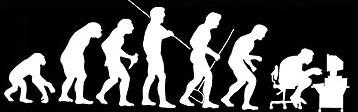
evolution (n) - gradual change to a different form
Posts: 5663
|
Yes, you can enter the PO to Joe's and manually enter the $20 price. If you enter it into the standard cost screen it will pull into the PO automatically, that's all. And will also correctly roll up into the total table standard cost. But if the cost of the lathe work fluctuates, then yes, manually entering the cost might be less work. In any event, the actual cost of the table will refect what is entered on the PO, not the standard.
|