Lynn_Pantic
Administrator
   
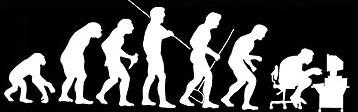
evolution (n) - gradual change to a different form
Posts: 5681
|
Last, Average and Standard can very well be all different because they represent different things. Average Cost is the weighted average of existing on-hand stock. New Average Cost is calculated when items are put into stock by averaging with what is there. If there is 0 on hand, a new average will begin. Transactions coming out of stock (including COGS of shipments take place at Average Cost. Last Cost is a reference only and is the cost associated with the last transaction adding to stock, from any source including the reversal of a transaction that would normally consume stock. Standard Cost is a benchmark and never changes until you deliberately change it. Standard Cost for purchased items is entered and then the standard cost of assemblies is rolled up based on the bill of materials, purchased component standard cost and, if applicable, labor and overhead based on time standards on routings and work center rates. If you use a work order to manufacture an assembly and issue the components to it per the Bill of Materials, the program will calculate the cost for you and WO-I will put the completed assembly into stock at the combined cost of components which will then become COGS when it ships. Timing is very important as well as preventing negative inventory if you want accurate costs.
|